Structural dynamics measurements
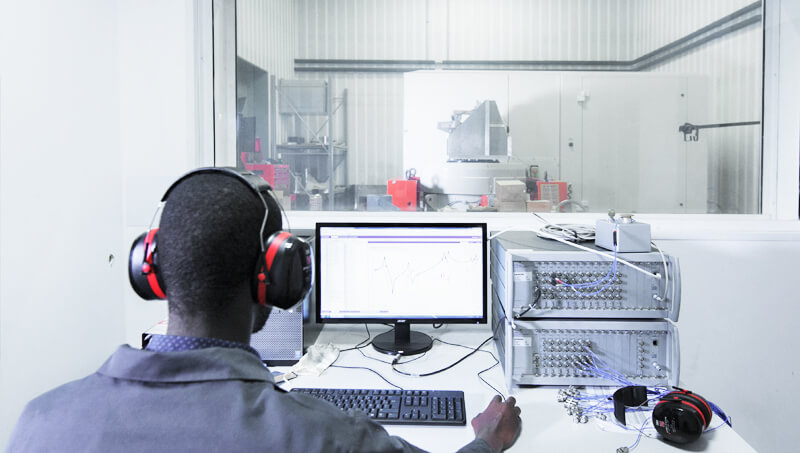
The CEVAA carries out structural dynamics measurements. We have extensive experience in the vibration measurement of structures to make a system more reliable or to validate its design.
Vibration measurement of structures
The CEVAA has 1D and 3D accelerometers as well as two 3D laser vibrometers (a PSV 400 and a PSV 500-Xtra). These different means allow the measurement for various cases:
- Modal analysis in free-free or measurement on a test plate using an impact hammer, a piezoelectric shaker, or a vibrating pot
- Measurement on an electrodynamic vibrator from 1kN to 125kN, for various excitation profiles (sine sweep, random, resonance frequency tracking (sine-Dwell), reproduction of time signals)
- Operational measurement (example: on a running engine, or on-road measurements)
All this on more or less large structures (from a microcomponent presenting an electronic card to a locomotive), and more or less complex (an airplane propeller to an electric motor).
Objectives
These measurements allow a better understanding of the vibration phenomena of a structure, whose objectives of these measurements can be:
- Identify resonances and associate these resonances with operational / modal distortions,
- Identifying critical regimes and associating them with operational distortions,
- Measure the dynamic deformation field using the 3D laser vibrometer,
- Validate the reliability of a part from a vibration point of view, or explain observed failure phenomena.
Correlation calculations / tests
Vibration measurements associated with simulation (one of CEVAA’s skills) allow a calculation/test correlation, including in particular:
- Digital model registration,
- Realization of MAC (Modal Assurance Criterion) between the tests and the calculation,
- Comparison of strain/stress field mapping in dynamics between calculation and tests.
- Making of a digital twin
The purpose of this calculation/test correlation is, on the one hand, to validate the numerical model from the tests and, on the other hand, to acquire a reliable model in order to iterate on the design of a product for materials which can be non-isotropic such as composites or parts from metal additive manufacturing.
OUR TECHNICAL MEANS
For more information, contact our teams!