Virtual testing
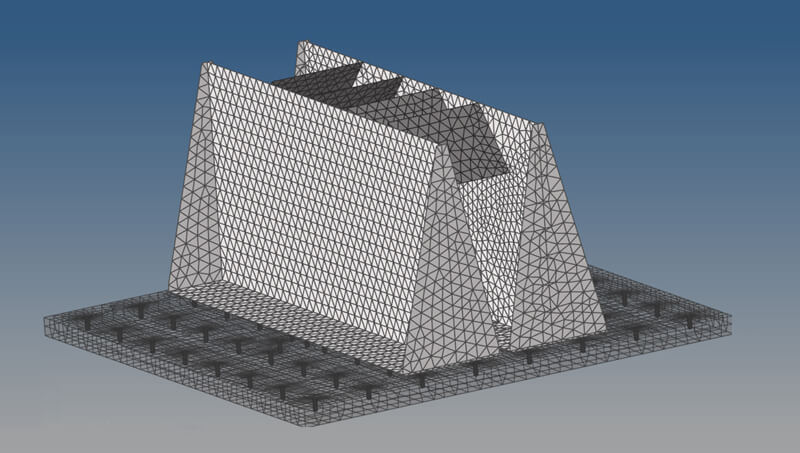
Raising the risk of failure on a tested part and its tools and anticipating measurements on a vibrator is made possible thanks to simulation and virtual testing.
Virtual vibration qualification tests for industry
Equipment vibration qualification requirements are gradually being extended to all sectors of industrial activity (automotive, aeronautics, rail, space, energy, etc.). Depending on the operational characteristics of the product and the constraints ; different types of excitation can be applied. The main types are endurance tests by sine sweep, random tests and tests by fixed sine excitation, or by monitoring a resonant frequency (sine dwell). Depending on the specifications and the number of specimens to be tested, the tests can last from a few hours to several weeks for the longest campaigns.
When the test leads to a failure of the tested product, it is then a question of analyzing the causes in order to review its design. A new prototype is then manufactured to be subjected again to the vibration qualification test.
This iteration necessarily impacts the project schedule and budget.
In the worst case, a single iteration is not always sufficient.
A real time saver for industry, the virtual test limits the number of experimental campaigns by selecting an optimized prototype via virtual tests carried out upstream.
Virtual derisking
In product validation plans, where keeping the schedule and respecting the budget are essential, it is very important to avoid any iteration phase on the physical prototype. Numerical modeling now offers all the functionalities needed to analyze and limit the risk of failure of a product subjected to a vibration endurance cycle.
This phase of derisking must be systematic before the launch of a test campaign. For this, the sequence of simulation and calculation steps, called the digital workflow, must be optimized.
The fatigue damage is then represented on all the components of the tested product. The analysis of all of these results leads to the conclusion that the product has infinite endurance or a number of cycles before failure. In the event of a risk of failure, the dynamic behavior of the product on its tooling is analyzed in detail and a product resizing phase can be launched.
In view of the cost and the consequences of an iteration on a physical prototype, iterations on a virtual prototype are clearly advantageous for the project and the customer.
6VIB : virtual tests solution
All the steps necessary for a virtual vibration endurance test have been implemented within the 6VIB solution. This solution developed by CEVAA and the 6NAPSE Group offers a competitive service with an optimized digital workflow.
Thanks to the use of the calculation/test correlation functionalities of 6VIB, the models were readjusted from the results of experimental modal analysis and operational measurements.
The 6NAPSE Group now has the material, software and human resources to support its customers throughout the value chain of the vibration qualification of industrial equipment.
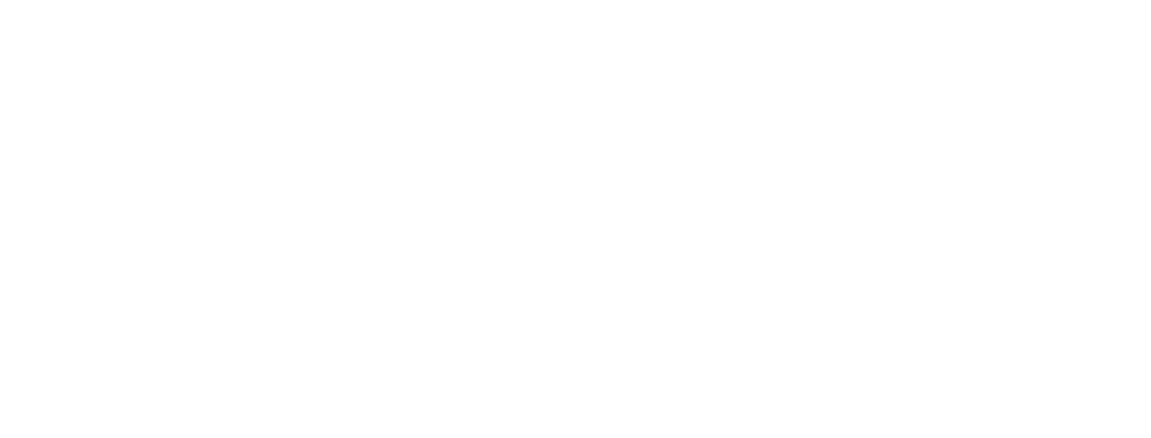
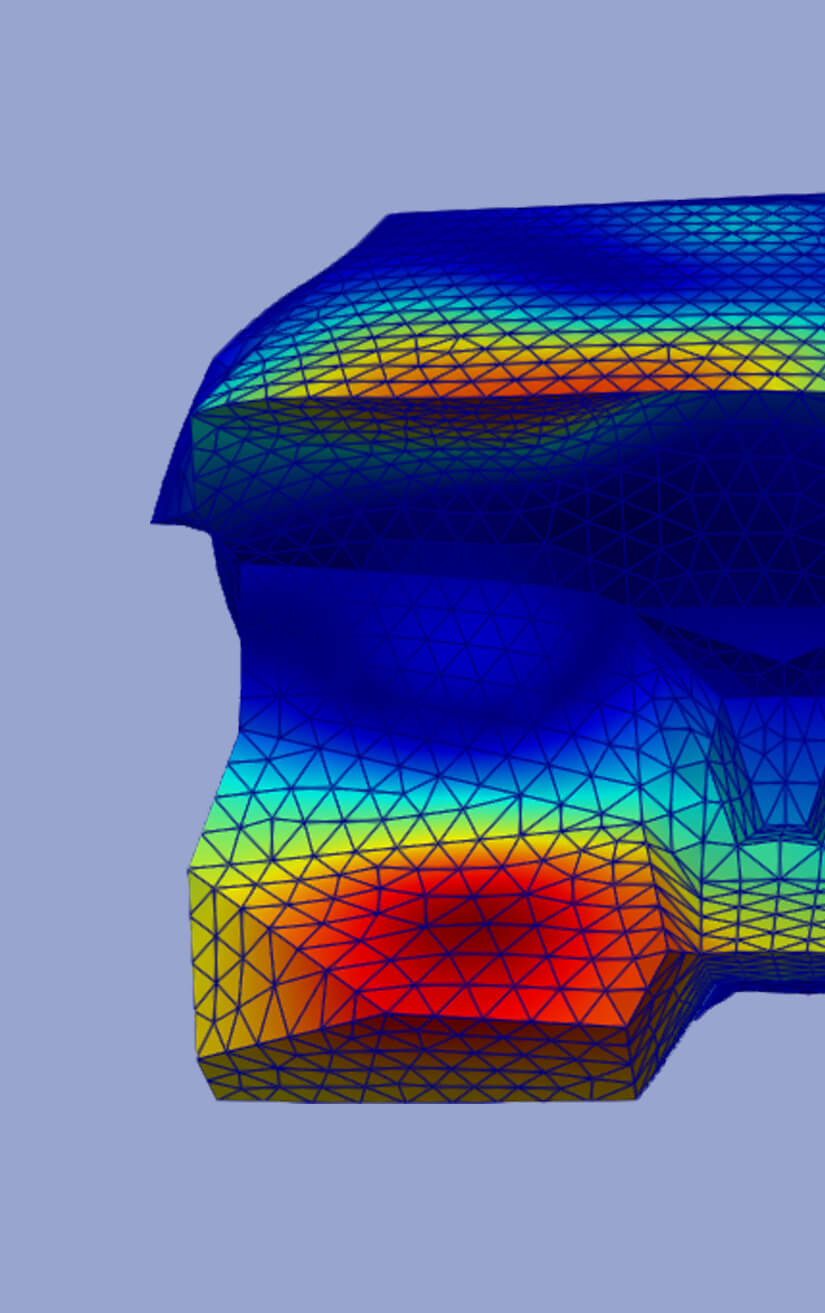
For more information, contact our teams!