Vibrhyss : predict and optimize acoustic comfort for the transportation industry
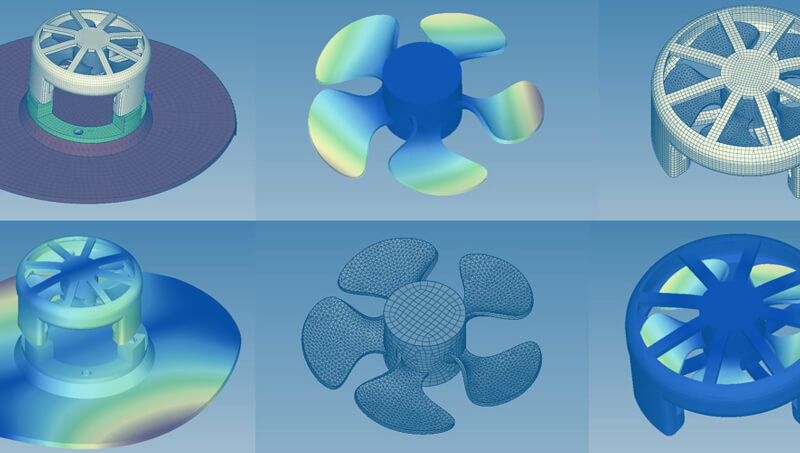
VIBRHYSS or how to take into account the acoustic performance when integrating a new vibration source through a hybrid Measurement/Calculations methodology.
Predict and optimize acoustic comfort for the transport industry
It is commonly accepted that the characterization of vibration sources is essential if one seeks to predict and optimize acoustic comfort on any type of structure intended for transport.
Car manufacturers have integrated expensive and effective digital methodologies allowing a complete characterization of active (vibration sources) and passive (body) components in order to optimize the noise generated by the main vibration sources (thermal engine, rolling noise, etc.). The purpose of our methodology is to propose a simplified approach, more economically accessible and dedicated to secondary sources.
Technical tests + digital modeling
The objective of this hybrid measurement/calculation methodology is to link measurements taken on the structure where the source will be implemented with a simple numerical model representing the connection between the source and the structure. Thus the optimization of the design of the connections (rigid or decoupled) can be carried out digitally in relation to the overall vibration and acoustic performance.
This methodology is intended to be deployed in design offices that do not have a vibro-acoustic digital model of the final product.
It will make it possible to deal more effectively with secondary sources of noise likely to degrade the standard of acoustic comfort of future electric or hybrid vehicles and therefore to comply with increasingly strict specifications.
For example, we applied this methodology in the case of an electric seat actuator. We measured the source (the motor), the transfer functions between the fixing of the actuator system and the comfort points. Then, we modeled the structural part that connects the engine to the seat and connected all of these elements. Thus, it was possible to iterate on a small model and optimize the acoustic and vibration levels at the comfort points.
Advantages of the Vibrhyss methodology :
- Connection of several elements (ex: seat/interface/actuator) for a reliable prediction of noise in the structure related to the new source
- Consideration of moments
- No need to scan all sets
- No prototype
- Applies to any source added to an existing structure